APPLICATION
How avoid "edge crack" of copper-aluminum composit
Editor :frank
Time :2018-09-11 17:15:00
Edge crack can be produced in hot and cold rolling.
Hot rolled edge crack:
Causes:
1. Low heating temperature of ingot
2. Poor metal plasticity
3. The side of the ingot has tissue defects
4. Hot rolling has high cooling intensity
5. Improper time of roller edge
6. Poor control of roll profile, resulting in cracks at the edge attached to the tensile stress
7. Low final rolling temperature
Elimination measures:
1. Change the heating and hot rolling process parameters according to the characteristics of the alloy, and increase the casting temperature appropriately
2. Reduce cooling lubrication
3. Use the roller edge one or two times in advance
4. Appropriately increase the final rolling temperature
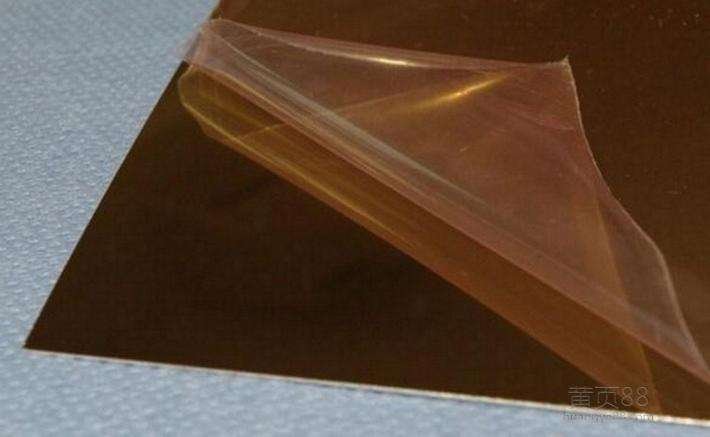
Cold rolled edge crack:
Causes:
1. There are cracks in the side of incoming material
2. Heavy grain of incoming material
3. High processing rate
4. High total processing rate
5. High rolling tension
Elimination measures:
1. Clean the cracks in the edge of incoming material
2. Reduce the processing rate of once. Generally, the processing rate of once shall not exceed 30% according to different equipment
3. When cold rolled to a certain extent, annealing should be done in a timely manner. The total processing rate of red copper and low-zinc alloys above H90 can exceed 90%.
4. Reasonably control the rolling tension to avoid cracking due to side defects when the tension is too high.
Hot rolled edge crack:
Causes:
1. Low heating temperature of ingot
2. Poor metal plasticity
3. The side of the ingot has tissue defects
4. Hot rolling has high cooling intensity
5. Improper time of roller edge
6. Poor control of roll profile, resulting in cracks at the edge attached to the tensile stress
7. Low final rolling temperature
Elimination measures:
1. Change the heating and hot rolling process parameters according to the characteristics of the alloy, and increase the casting temperature appropriately
2. Reduce cooling lubrication
3. Use the roller edge one or two times in advance
4. Appropriately increase the final rolling temperature
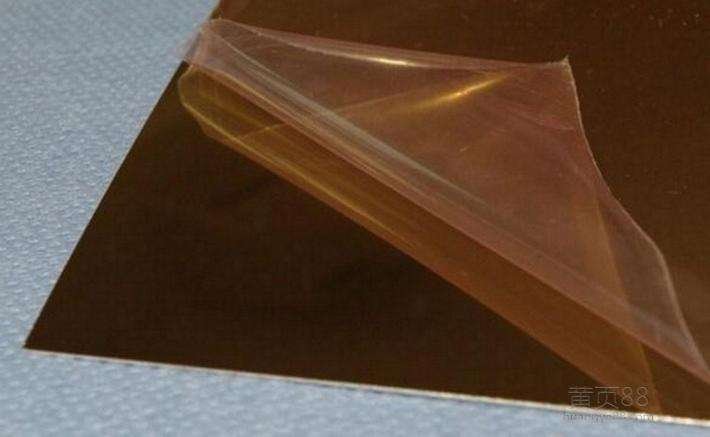
Cold rolled edge crack:
Causes:
1. There are cracks in the side of incoming material
2. Heavy grain of incoming material
3. High processing rate
4. High total processing rate
5. High rolling tension
Elimination measures:
1. Clean the cracks in the edge of incoming material
2. Reduce the processing rate of once. Generally, the processing rate of once shall not exceed 30% according to different equipment
3. When cold rolled to a certain extent, annealing should be done in a timely manner. The total processing rate of red copper and low-zinc alloys above H90 can exceed 90%.
4. Reasonably control the rolling tension to avoid cracking due to side defects when the tension is too high.
Related :
- Copper-Aluminium Bimetal Clad Sheet2023-04-27
- Bimetallic copper aluminum washers2020-06-30
- copper-aluminium bimetal clad sheet2020-07-08
- copper coated aluminium busbar2021-03-01
- aluminum copper clad laminate sheet2021-03-15
- is copper clad aluminum wire good?2021-03-30